Compression load cells are essential components for industries that require accurate force measurement and weight monitoring. These devices convert mechanical force into an electrical signal, offering precise and reliable readings. Widely used in manufacturing, healthcare, and other sectors, compression load cells ensure critical processes are carried out with precision.
This comprehensive guide explores the features, benefits, and innovations of compression load cells, highlighting their transformative impact across various industries.
What Are Compression Load Cells?
How They Work
Compression load cells operate using strain gauges. When a force is applied, the internal structure compresses slightly, causing the strain gauges to detect changes in resistance. These changes are then converted into electrical signals, providing accurate measurements of the applied force.
Key Materials and Design
Compression load cells are made from high-strength materials like stainless steel and aluminum, enabling them to handle heavy loads while resisting environmental challenges such as corrosion and temperature fluctuations. Their robust construction and compact design make them ideal for high-capacity applications in challenging environments.
Features That Define Compression Load Cells
High Accuracy Levels
Compression load cells are designed to deliver highly accurate measurements, even in demanding conditions. Their sensitivity and consistency make them a trusted choice in industries requiring precise performance.
Versatility Across Applications
The adaptability of compression load cells allows them to be used in diverse settings, from industrial weighing systems to medical devices. Their ability to function reliably under varying conditions has made them indispensable in many sectors.
Long-Lasting Durability
These devices are engineered for durability, ensuring consistent performance over time. Their resistance to mechanical stress, extreme temperatures, and environmental factors enhances their longevity and reliability.
Applications of Compression Load Cells
Industrial Weighing Systems
Compression load cells play a crucial role in industrial weighing systems, including silos, hoppers, and tanks. They provide precise weight measurements for raw materials, enabling efficient inventory management and reducing production waste.
Medical Devices and Equipment
In healthcare, compression load cells are used in devices such as patient lifts, infusion pumps, and surgical robots. Their precision ensures safety and reliability in medical procedures, contributing to better patient outcomes.
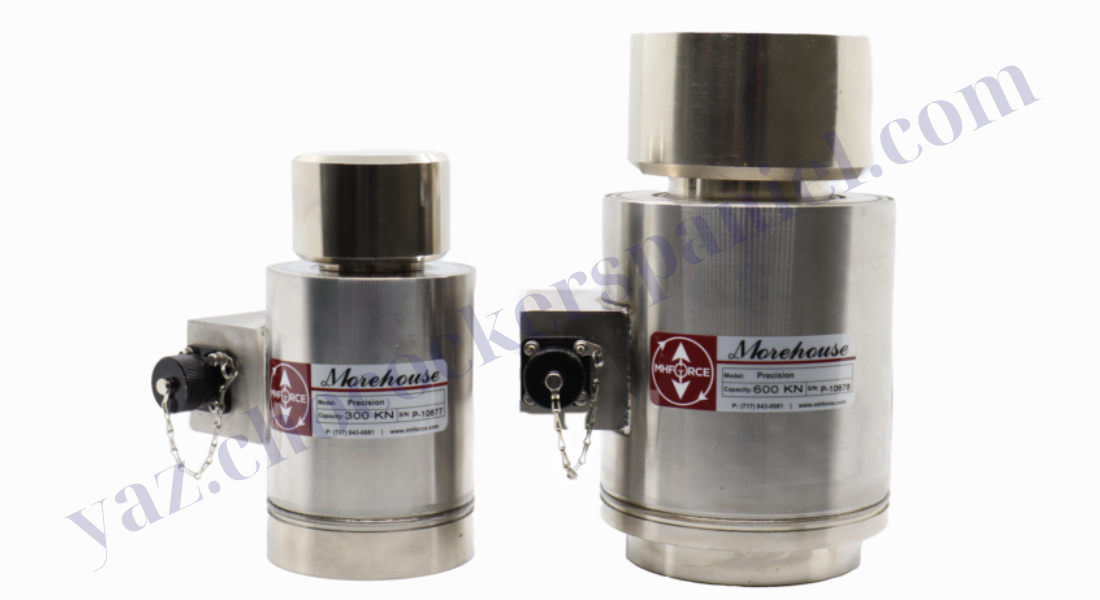
Aerospace and Automotive Testing
Compression load cells are critical for testing the performance and durability of aerospace and automotive components. They measure forces during simulations, ensuring the reliability and safety of critical parts under real-world conditions.
Renewable Energy Systems
Compression load cells are widely used in renewable energy applications like wind turbine monitoring and solar panel tracking. They ensure optimal performance by measuring mechanical forces and maintaining system efficiency.
Benefits of Compression Load Cells
Improved Operational Efficiency
By delivering accurate force and weight measurements, compression load cells enhance process efficiency. This leads to better resource utilization, reduced errors, and streamlined workflows, especially in high-demand industrial environments.
Cost-Effective Solutions
Although the initial investment in compression load cells may be significant, their durability, low maintenance requirements, and reliable performance make them a cost-effective solution over time.
Enhanced Safety Measures
Compression load cells contribute to workplace safety by monitoring loads and preventing overload situations that could cause equipment failure or accidents. Their role in ensuring operational safety is invaluable.
Innovations in Compression Load Cells
Digital Load Cells
Modern compression load cells feature digital capabilities, enabling real-time data transfer and remote monitoring. These advanced devices integrate seamlessly with automated control systems, enhancing efficiency and decision-making.
Miniature Load Cells
Miniature compression load cells are designed for applications that require precise measurements in compact spaces, such as robotics and consumer electronics. Despite their small size, they deliver high levels of accuracy.
High-Capacity Models
High-capacity compression load cells are designed to handle substantial forces without compromising on precision. These models are particularly useful in industries like construction and shipping, where heavy loads are common.
IoT Integration
The integration of IoT technology into compression load cells allows for continuous data collection and analysis. These devices enable predictive maintenance, improved operational control, and smarter decision-making by connecting to cloud platforms.
Choosing the Right Compression Load Cells
Understanding Load Requirements
Selecting the right compression load cell starts with determining the maximum load it will measure. Choosing a device with a load capacity higher than the anticipated maximum ensures accuracy and prevents overloading.
Evaluating Environmental Conditions
Environmental factors such as temperature, humidity, and exposure to corrosive substances can impact load cell performance. It is essential to choose a model designed to withstand the specific conditions of your application.
Assessing Output and Compatibility
Different applications require various output signals, such as analog or digital. Ensure that the chosen compression load cell is compatible with your system’s requirements to avoid integration challenges.
Balancing Budget and Features
While advanced features may enhance performance, they may not always be necessary for every application. Balancing your budget with the required features helps you select the most suitable compression load cell for your needs.
Leading Providers of Precision Load Cells
Flintec
Flintec is recognized for its expertise in developing highly accurate force measurement solutions. Catering to sectors such as healthcare, aerospace, and industrial weighing, their products are renowned for robust construction and advanced technology. Their focus on innovation ensures reliable performance across diverse applications.
HBM
HBM delivers exceptional performance in force measurement, with a portfolio featuring both digital and analog devices. Their solutions are designed for demanding environments, making them a top choice for industries requiring precision and durability.
Vishay Precision Group
Vishay Precision Group offers an extensive range of devices tailored for construction, automotive, and manufacturing sectors. Their products are valued for their high accuracy, resilience, and consistent performance, ensuring long-term reliability in critical applications.
Best Practices for Maintaining Measurement Devices
Routine Calibration
Regular calibration is essential for maintaining the accuracy and consistency of these devices. Scheduling periodic checks minimizes performance drift and ensures precise readings throughout their lifespan.
Cleaning and Regular Inspections
Clean these measurement tools with a soft cloth to remove dust and debris, avoiding harsh chemicals that may damage their surface. Frequent inspections help identify potential issues like wear or corrosion, enabling timely repairs or replacements.
Ensuring Proper Installation
Correct installation is critical for optimal performance. Following the manufacturer’s guidelines during setup ensures the devices operate efficiently and maintains their longevity.
Mitigating Environmental Impact
Protecting these devices from extreme conditions enhances their performance. Using protective covers or enclosures can shield them from harsh environments, extending their usability and maintaining accuracy.
Innovations and Trends in Force Measurement Solutions
AI-Enhanced Performance
Artificial intelligence is revolutionizing how these devices operate. AI-powered analytics provide real-time insights, optimizing performance, forecasting maintenance needs, and improving operational efficiency.
Tailored Designs for Industry Needs
Customization is becoming increasingly important, with manufacturers creating solutions designed to meet specific industry challenges. Tailored products ensure compatibility and efficiency, offering enhanced functionality for unique applications.
Eco-Friendly Innovations
Sustainability is a growing focus, with manufacturers integrating recyclable materials and energy-efficient designs. These advancements align with global efforts to reduce environmental impact while maintaining performance.
IoT Integration for Smarter Systems
The incorporation of IoT technology is expanding the capabilities of these devices. Real-time data monitoring and cloud connectivity enable smarter systems that improve decision-making, predictive maintenance, and operational control.
Closing Thoughts
Precision force measurement devices are driving advancements across industries, providing reliable and accurate solutions for diverse applications. Their adaptability and durability make them invaluable tools in sectors such as manufacturing, healthcare, and construction.
As technology evolves, these tools continue to improve, integrating smarter features and sustainable practices. Investing in quality devices ensures operational efficiency, enhanced safety, and long-term value, solidifying their role as essential components in modern systems.